China National Heavy Duty Truck Jinan Casting and Forging Center MP8000 hot forging press automatic production line mainly produces universal joint forgings, the production line introduces SMS company bus control technology and technology, the main machine is imported from Germany, high degree of automation, stable cycle, high product quality, The output is large and belongs to the world-class production line. In the forging production of universal joints, it is often the case that the lower top rod cannot be returned, resulting in the discontinuation of batch waste. In response to this problem, solutions need to be found in the production process to ensure stable operation of the production line and production of qualified products.
First, the problem is raised and analyzed
Since the topping material generally adopts the top forging part during the forging process of the universal joint, the lubricant, the oxide scale and the cooling water will flow into the cavity of the lower mold part during the use of the mold, and forging a class will be The result is that the top rod of the mold and the mold box is blocked by graphite and oxide scale, which causes the top rod to not return smoothly or even return to the position. It is reflected that the universal joint has insufficient length, and if it is not timely, it may be Bulk waste will appear. At the same time, if the equipment top rod is not cleaned in time for a long time, the mold box cannot be pulled out, which seriously affects the production line production.
Second, the problem is solved
Since the MP8000 production line is automated, with fast tempo and large output, it is necessary to find a suitable method to solve the problem of clogging the top rod in production. The current countermeasures in production are as follows.
1. Seeking reasonable graphite ratio
In the forging process, the lubrication of the lower mold is very important. In order to improve the service life of the mold and ensure the quality of the product, a higher concentration of lubricant should be selected, and in order to avoid the blockage caused by excessive concentration of the lubricant, it is necessary to control the graphite concentration. Reasonable concentrations must be selected in production to achieve lubrication, demoulding and prevent clogging balance (see Figure 1). After long-term practice, select a graphite concentration of 1:10.
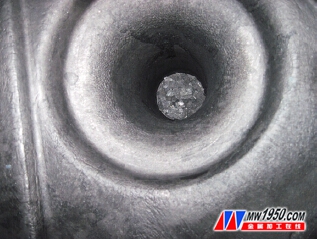
Figure 1 Lowering the model cavity after purging and spraying graphite
2. Maintain a good purging effect
Before the mold is cooled and lubricated, the oxide inside the cavity is blown away, which is an important part of reducing the clogging, ensuring that the purge line is smooth and the nozzle direction is correct and reasonable, which is necessary preparation before each shift.
3. Forgings are long and regular inspections
With the production, the returning position of the top rod can be completely reflected by the online inspection. When the trend of the downward trend is changed, the sampling frequency should be increased, and the situation close to the lower one should be taken immediately. Clean the furnace or stop the line to avoid bulk waste (see Figure 2).
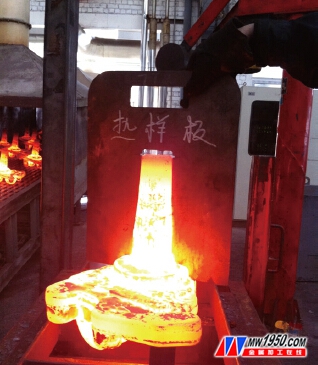
Figure 2 Using the inspection template to quickly check the gimbal length
4. Thoroughly clean when changing the mold
(1) Cleaning of the mold top rod Since the mold box can only discharge graphite from the top hole, the mold top rod is also easily blocked by graphite, and should be thoroughly cleaned each time the mold is replaced.
(2) Equipment pad ejector rod cleaning After the MP8000 main engine has been forged for a long time, the workpiece deposits a large amount of graphite on the top rod and the flange of the bottom plate. Due to the accumulation of graphite, the ejector rod is not returned smoothly, and the mold is replaced. The mold cannot be safely pulled out. In order to safely and smoothly return the top rod when changing the mold, the top rod must be cleaned when installing the top rod, as shown in Figure 3 and Figure 4.
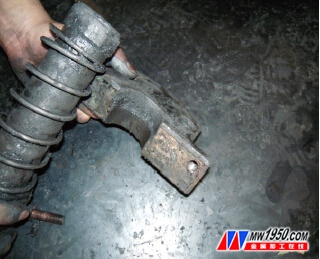
Figure 3 Dip with graphite equipment pad ejector rods, flanges
and springs
Figure 4 Cleaning the equipment pad ejector rods, flanges and springs
(3) Cleaning the top rod of the equipment: 2~3 people cooperate to remove the top rod, put two pieces of sleepers on the ground, put the top rod on the sleepers; use a small shovel to clean the deposited graphite on the top rod; The brush is cleaned twice with water and wiped clean with a rag; for graphite and rust that are difficult to clean on the top rod, clean it with a grindstone and kerosene, then wipe it twice with a rag and finally blow it dry with compressed air. Apply 2# lithium base grease before loading, as shown in Figure 5 and Figure 6.
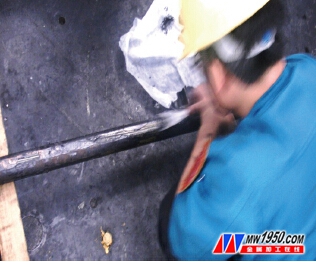
Figure 5 Before the top rod is cleaned
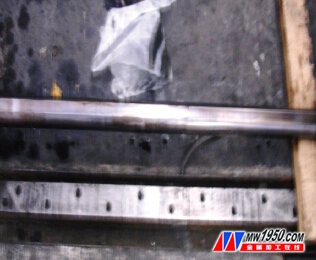
Figure 6 After the top rod is cleaned
5. Attempts to produce new methods
Recently, MP8000 forging die forging and final forging die top bar has been frequently blocked by graphite, resulting in the top bar not returning, directly affecting the length of the forging, resulting in some defective products and individual waste. Because the current graphite concentration should not be reduced, and the purge is normal, through on-site observation, it is easy to stop the forging bar after the forging and production of the mold for a long time, so it is easy to see that the top rod does not return. Therefore, it should be considered that there is a link with the baking mold. Larger relationship. That is, since the baking mold will dry the graphite remaining in the cavity, it is obviously caused that the ejector rod is not blocked.
In the case that the production task does not allow long-term stoppage for cleaning, we propose the following scheme: after forging the last universal joint in the production line, set the automatic spray graphite time to 0, so that the cavity does not There will be graphite.
The method of washing the mold with boiling water is taken before the mold is baked after the mold is repaired. The details are as follows: During the stop of MP8000 production, after the equipment flywheel stops and the mold is repaired, the pre-forging and final forging die are injected with boiling water, and the topping mechanism is repeatedly operated every 30s1 times until the boiling water flows smoothly out of the lower mold. . Then arrange the baking mold work.
After two months of operation observation, this method is simple and practical, which greatly reduces the number of occurrences of the lower top rod not returning.
Third, the conclusion
Due to the process reasons, there is no means to completely avoid the problem of the topping material not returning to the position; the automated production line should pay close attention to the long change of the forgings to prevent the occurrence of batch waste; when the production line replaces the tooling mold, the topping of the mold box is cleaned. It is an extremely important task, which must be carried out in earnest; regular cleaning of the equipment top rod can ensure the long-term normal operation of the press; during the production of a set of mold tooling, the hot water washing method can greatly reduce the lower top rod. The occurrence of the return problem is worth promoting in production.
   About the author: Zhu Xi, Zhao Chunxia, ​​Li Shuai, China National Heavy Duty Truck Jinan Casting and Forging Center, forging one.
Cutting Wheels
Fiberglass Nets is punched from fiberglass cloth for grinding wheel after coating with phenolic and epoxy resin and curing by heating ..
It is the best base material for resin bond grinding wheel with the features of high tensile strength and deflection resistance
There have two kind of weave: plain weave and leno weave.
Surface: with black paper(P) or wax paper or non-woven fabric.
Item: Cutting Disc,Grinding Disc
Warranty: 3 years
Customized support: OEM, ODM, OBM
Place of Origin: China
Model Number: Various as per customer requirements.
Type: Cutting Disc,Abrasive Disc
Application: Cutting tool for stainless steel and metal
Material: Aluminum Oxide
Bond: Resin
Color: Black/Green/Brown/Customized
OEM: Yes
Diameter: 4-16 Inch
Style: Abrasive Disc
SUPPIER OF Material:
SAINT-GOBAIN is the the world's top500company which offer best alumina
powder.
Phenolic Resin: lt is the most import-ant part of cutting wheel,we use the best suppliers of the word.
Uality is the first:The fiberglassnetwe use more strong material, we believe quality is the live of a company.
No Rusting Metal Ring: For strong embedded ability, our metal ring with our new technology, it will no rusting, and no fall down.
The related abrasive products we can supply is Flap Disc Adhesive , Flap Disc Backing Pad, Abrasive Flap Disc , and Abrasive Machine such as Flap Disc Making Machine, Abrasive Belt Making Machine, Flap Wheel Machine , Sanding Disc Machine, if you have any needs about abrasive tools, please kindly feel free to contact us.
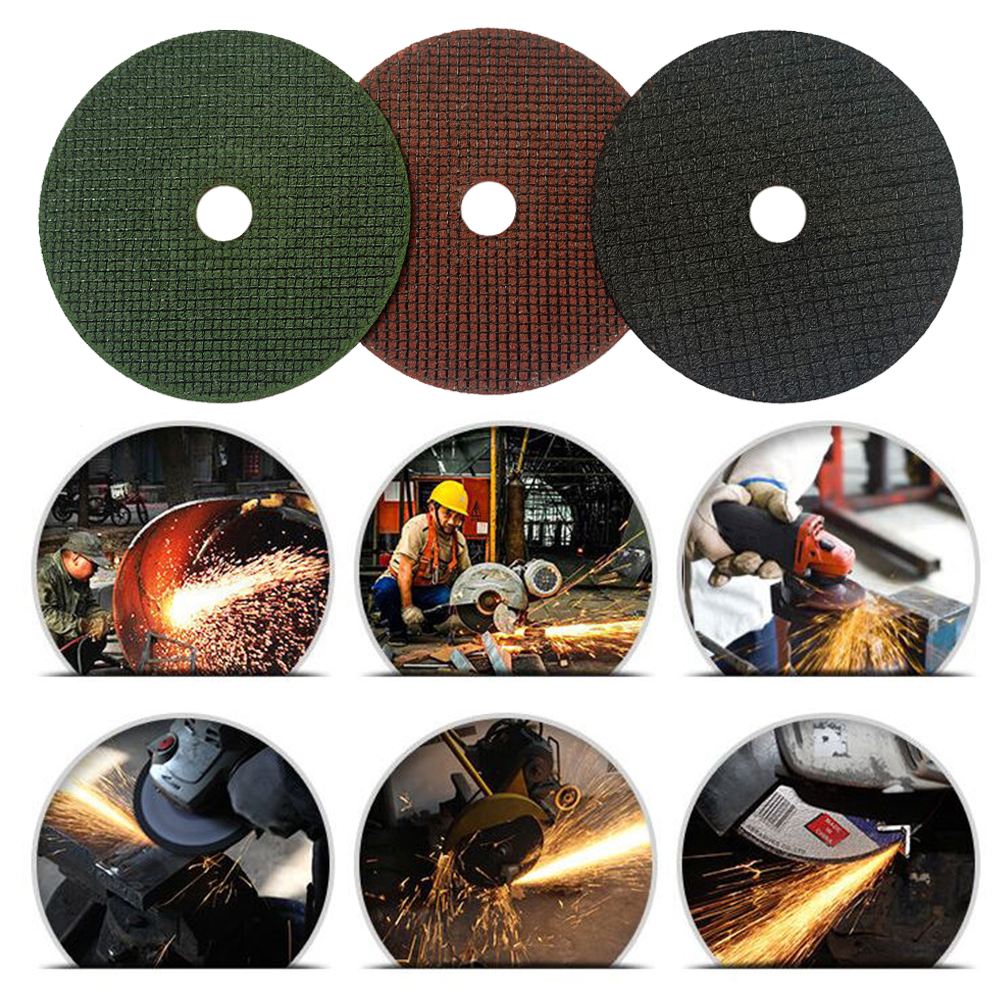
Cutting Wheels,abrasive cutting disc,Metal Cutting Disc,Thin Cutting Disc,Metal Cutting Wheels
Zhengzhou Jiading Abrasive Manufacturing Co.,Ltd , https://www.jiadingabrasive.com