First, the application status of solid wire in our company
Our company's business is mainly based on petrochemical engineering construction and equipment manufacturing. The solid wire is relatively cheaper than the flux-cored wire. Especially the domestic welding wire commonly used in carbon steel and low-alloy steel products has the advantages of low price, high construction production efficiency and stable product performance, which makes the solid wire widely used. The solid wire is mainly used in the welding construction of many steel products such as containers, towers, heat exchangers, pipes, storage tanks, steel structures and wind towers, as shown in Figure 1 and Figure 2. Among them, the solid core welding wire with the most application of carbon steel and low alloy steel products is E R50-6; the solid core welding wire used in stainless steel and stainless steel composite products is H03C r21N i10S i (E R308L), H03C r24N i13S i (E R309L), H03C r19N i12M o2S i (E R316L) and H08Cr20Ni10Nb.
Second, application examples and problems
1. Application of solid wire in the welding of carbon steel and low alloy steel
Our company's most commonly used solid wire in carbon steel and low alloy steel products is E R50-6, which uses a single component CO 2 as shielding gas, large splash, weld forming protrusion, pore and undercut. Such problems have always restricted the application range of solid wire. In recent years, product users have continuously compressed the manufacturing cycle of products. Traditional electrode arc welding has been unable to meet the current construction production requirements. The construction cost of flux cored wire is relatively high, prompting the adoption of effective measures to solve the solid core. The problem of large splashing and poor forming of the welding wire enables the solid wire to be applied to welding equipment such as pressure vessels.
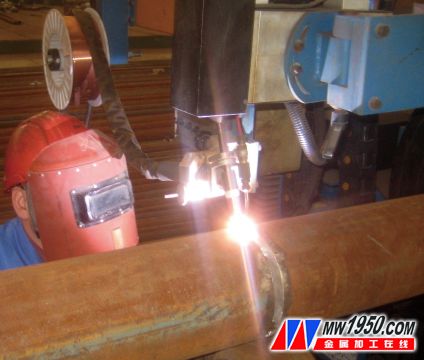
Figure 1 Application of solid wire in automatic pipe welding
The main countermeasures are as follows: First, select the appropriate power polarity and welding parameters, and the welding speed is adjusted according to the selected welding current, arc voltage and welding position. Adjusting the inclination angle and welding direction of the welding torch during welding, the inclination angle of the gun body is too small (perpendicular to the workpiece) is unfavorable for the welding operator to observe the formation of the weld bead; if the inclination angle of the gun body is too large, a large amount of splash will be generated during welding. After repeated adjustments, in the welding direction, the right welding method (the welding wire points in the opposite direction of the welding surface) is more advantageous than the left welding method in the stability and the amount of the arc. The length of the wire is controlled to be as short as possible in the case of normal welding.
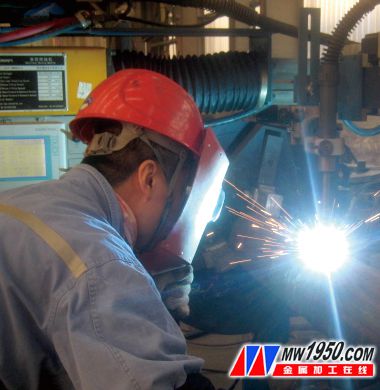
Figure 2 Application of solid wire in CO 2 gas shielded welding
Second, for some materials, a single CO 2 shielding gas can be changed to the mixed gas Ar + CO 2 , and the CO 2 + A r mixed gas can also improve weld formation in addition to overcoming the splash. It has been proved that the spatter rate is lower when 80% Ar+20% CO 2 .
Third, the use of domestic well-known brands and the most advantageous manufacturers of solid wire manufacturing manufacturers of welding consumables. Under the premise of ensuring the mechanical properties, the carbon content should be reduced as much as possible, and an appropriate amount of alloying elements such as titanium and aluminum should be added. Whether particle transition welding or short-circuit transition welding can significantly reduce splashes caused by gases such as CO 2 (see Figure 3).
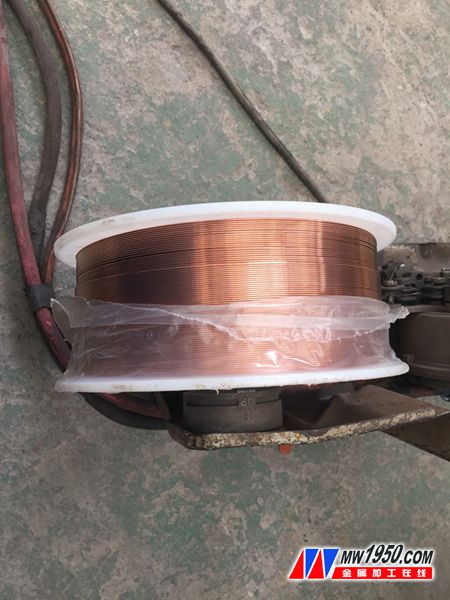
Figure 3 Good quality solid wire (Bridge ER50-6)
Fourth, select a welder with appropriate electrical characteristics. Apply a certain amount of anti-splash agent to the sides of the weld before welding to reduce the difficulty of removing the splash.
2. Application of solid wire on nickel-based high alloy steel
Our company encountered the problem that the metal color of the weld surface did not meet the requirements when welding the N08825 pipeline material (the surface of the weld was dark and excessively oxidized), and the surface of the weld after pickling still could not meet the requirements. This problem is concentrated in the entire weld of the back seal weld of the large diameter pipeline material and the small diameter thin wall joint. The welds in the above positions are welded by tungsten inert gas welding, and the welding material is made of solid core ERNiCrMo-3 material.
Test and take measures from the following aspects:
(1) Insufficient protective gas or insufficient purity The protective device has been redesigned to increase the coverage of the protective gas. After re-testing after adjustment, although the weld oxidation situation has improved, it still cannot meet the technical requirements. The purity of the shielding gas is not required to cause excessive oxidation of the surface of the weld. Since the purity standard of 99.99% argon (domestic) has been used before, it is not considered in this respect. According to the expert's suggestion, we purchased the welding protective gas of the liquid liquid (one bottle of 99.99% A r and 9 5 % A r + 5 % H 2 ) for the welding test. The test effect is very satisfactory, completely solves the problem of serious oxidation of the weld surface. The welding of imported protective gas shows that the appearance of the weld is bright silver, which fully meets the requirements.
(2) The welding consumable factor may be due to the welding material itself affecting the degree of oxidation of the weld. On the one hand, we actively contact with well-known domestic welding consumables manufacturers to change the manufacturing formula of welding consumables to improve the serious oxidation of the weld surface; on the other hand, we imported the same type of welding consumables from some well-known manufacturers for welding tests. The problem has not been resolved after many trials.
Third, the problems in the use of domestic solid wire
(1) The warpage distance of the domestic welding wire is large, affecting the effect of wire feeding and the welding quality. When the warpage is large, the wire and the wire tube are rubbed to increase the wire feeding resistance. It is related to the straightening in the wire production, and is used abroad. The welding wire (φ 1.2mm) warp distance is generally <5m m, the warping distance of the welding wire produced by Kobelco in Japan is almost zero, and the warping distance of the domestic welding wire is less than 5mm. The welding often causes the weld to be inferior, which affects the weld. Quality, but has to be polished, directly resulting in inefficient work.
(2) Copper plating quality of welding wire At present, copper plating of welding wire adopts two methods of electroless plating and electroplating. The electroless plating has low cost, small porosity, low bonding strength of the plating layer, high electroplating cost, large porosity, and high bonding strength of the plating layer. Japanese welding wire is generally electroplated, Western Europe is electroless plating, China is mainly electroless plating, and a few manufacturers use electroplating.
Domestic copper-plated welding wire has problems such as uneven copper plating layer, poor bonding force, easy to remove copper chips, easy rusting of copper plating layer, and short storage time.
(3) Less welding wire manufacturers such as nickel-based surfacing In recent years, with the adjustment of the product structure of the enterprise, the welding metal materials range from common Q235 and Q345 to high-strength steel, high-toughness steel and heat-resistant steel (such as 12C r2M o1V). ) and other fields are expanding, and there are very few manufacturers of such wire in China. The product quality is often unstable, the process is not up to standard, the price is too high, and the production requirements cannot be met. Some special steel wire types still rely on imports. In actual production, for the welding of the above steel grades, sometimes only the imported welding wire or the welding process is changed.
Fourth, the need and recommendations for the development of solid wire
At present, the production of solid wire in China is limited by many factors, the technical level is limited, some low-end welding wire is made in China, the high-end solid wire is less domestically produced, and the operating performance is far less than the imported wire. The welding method of solid wire meets the requirements of high quality, automation, low cost and environmental protection for welding production. The future development of solid wire should start with raw materials. If the quality of the link cannot be firmly controlled, the localization of high-end solid wire will be difficult to develop. In addition, the welding protective gas matched with the solid core wire lacks the corresponding inspection and detection means in terms of purity and impurity inspection. Especially when encountering alloy materials sensitive to gas purity, the disadvantage of the solid core wire will be highlighted. Therefore, in order to further develop the solid wire, it is necessary to solve the above problems.
1. Align with the development of international welding materials technology
We should gradually phase out low-quality and inferior products, preferably good welding wire raw materials, strengthen the research on gas-shielded solid-core welding wire manufacturing technology, fully grasp the technical characteristics of imported equipment, continuously improve the variety and quality of raw materials, and formulate reasonable wire drawing, copper plating, layer winding and Packaging and other production process rules, completely solve the problem of quality stability of wire production, and produce high-quality welding materials for the production of more important products, so that the structure of solid wire in China tends to be reasonable.
2. Strengthen exchanges and collaboration to improve the overall manufacturing level of domestic solid wire
Domestic welding wire manufacturing enterprises should continuously strengthen exchanges and cooperation with each other, especially to strengthen cooperation between scientific research units, welding wire factories and users, and give full play to the advantages of all parties, so that the quality and variety of China's solid wire are continuously obtained. improve.
Throughout the development of gas-shielded solid wire at home and abroad, there is still a big gap between China and industrialized countries. This requires the joint efforts of the welding industry to develop high-quality wire products as soon as possible to better Adapt to the continuous development of China's welding production.
About the author: Yin Yiyue, etc., China Petroleum and Natural Gas Seventh Construction Company.
Related product links:
Air Liquide's ARCAL15 (95% A r + 5% H2) mixture is used in TIG welded austenitic stainless steels and nickel based alloys. High-quality welds are finally achieved through precise compounding and high-purity gases. Among them, H2 is a highly reductive chemical substance. The small amount of H2 contained in the welding shielding gas can preferentially react with oxygen trapped in the high temperature region of the welding to protect the weld metal from oxidation and exhibit silver-white metal. luster. Moreover, H2 has the characteristics of high thermal conductivity, which can increase the welding speed by about 30% compared with pure argon.
gas stove burner cover,Burner Cover,gas burner cover,household gas stove burner cover,part of burner
GUOLONG PRECISION VALVE CO.,LTD , https://www.glstovevalve.com